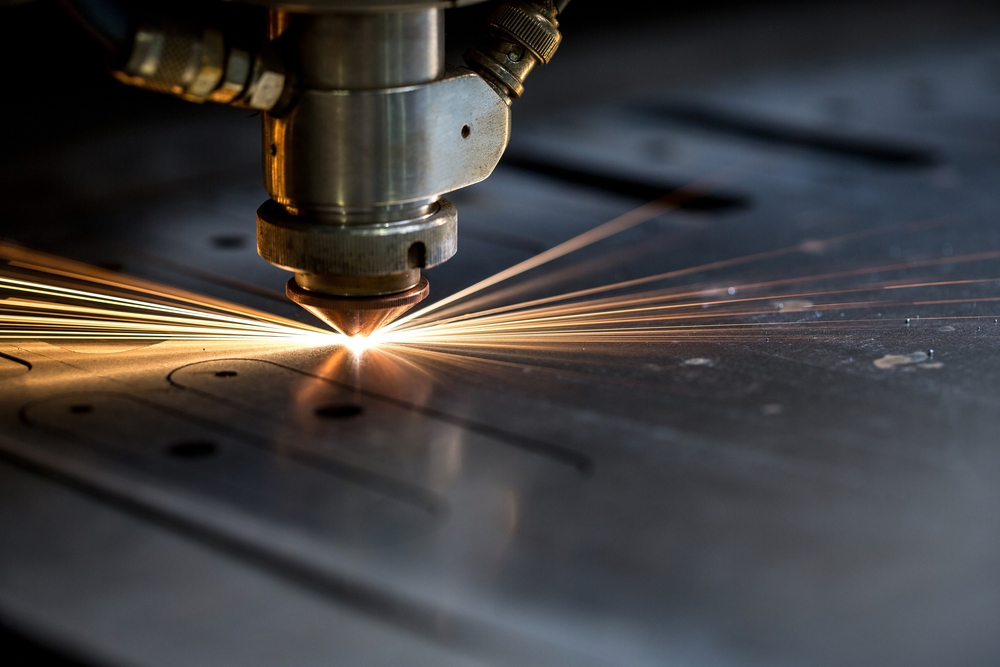
Metal machining is a cornerstone of modern manufacturing, enabling the creation of intricate components used across industries, from automotive to aerospace. This beginner’s guide will help you grasp the fundamentals of metal machining, including its techniques, tools, and applications.
What Is Metal Machining?
Metal machining refers to the process of removing material from a workpiece to achieve a desired shape, size, and finish. Using specialized tools and techniques, machinists transform raw metal into precise components. The machining process typically involves cutting, drilling, milling, and turning operations.
Importance of Metal Machining in Manufacturing
Metal machining is essential for:
- Precision: Creating components with exact dimensions and tolerances.
- Versatility: Working with a wide range of metals, including steel, aluminum, and titanium.
- Customization: Designing unique parts for specific applications.
Common Types of Machining Techniques
Understanding machining techniques is crucial for beginners. Here are the primary methods:
Turning
Turning involves rotating the workpiece against a stationary cutting tool, typically on a lathe. This process is ideal for creating cylindrical parts like shafts and rods.
- Tools Used: Lathe, cutting tools, and chucks.
- Applications: Automotive components, aerospace shafts, and industrial rollers.
Milling
Milling uses a rotating cutting tool to remove material from a stationary workpiece. It is versatile and can create flat surfaces, slots, and complex shapes.
- Tools Used: Milling machines, end mills, and face mills.
- Applications: Engine parts, molds, and gears.
Drilling
Drilling creates holes in the workpiece using a rotating drill bit. It is one of the simplest yet essential machining techniques.
- Tools Used: Drill press, twist drills, and boring bars.
- Applications: Fastener holes, pipes, and structural components.
Grinding
Grinding achieves a high level of precision and surface finish by using an abrasive wheel to remove material.
- Tools Used: Bench grinders, surface grinders, and cylindrical grinders.
- Applications: Tool sharpening, finishing parts, and smoothing surfaces.
Essential Tools and Equipment for Metal Machining
Equipping yourself with the right tools ensures effective and accurate machining. Here are the essentials:
Lathes
Lathes are indispensable for turning operations, enabling the creation of symmetrical shapes.
- Features: Adjustable speed, tool holders, and chuck systems.
- Popular Types: Engine lathes, CNC lathes, and turret lathes.
Milling Machines
Milling machines handle complex machining tasks, offering versatility for various materials and designs.
- Features: Variable speed control, tilting head, and multi-axis capabilities.
- Popular Types: Vertical milling machines, horizontal milling machines, and CNC mills.
Drill Presses
Drill presses provide stability and precision for drilling tasks, ensuring consistent results.
- Features: Depth stops, adjustable tables, and multiple speed settings.
- Applications: Used in woodworking and metalworking projects.
Measuring Instruments
Accurate measurements are vital for successful machining. Key instruments include:
- Calipers: Measure internal and external dimensions.
- Micrometers: Provide high-precision measurements.
- Dial Indicators: Ensure alignment and runout accuracy.
Materials Commonly Used in Metal Machining
Different metals exhibit unique properties that influence machining processes. Selecting the right material is crucial for achieving desired results.
Steel
Steel is widely used due to its strength, durability, and versatility. It is ideal for components requiring high wear resistance.
- Types: Carbon steel, stainless steel, and tool steel.
- Applications: Structural parts, tools, and machinery.
Aluminum
Aluminum is lightweight, corrosion-resistant, and easy to machine, making it suitable for aerospace and automotive applications.
- Applications: Aircraft parts, engine components, and consumer electronics.
Titanium
Titanium offers excellent strength-to-weight ratio and corrosion resistance but can be challenging to machine.
- Applications: Medical implants, aerospace components, and high-performance equipment.
Brass and Copper
These materials are soft and easy to machine, often used for decorative and electrical purposes.
- Applications: Electrical connectors, plumbing fixtures, and artistic designs.
Understanding Machining Parameters
Optimizing machining parameters ensures efficiency and quality. Beginners should familiarize themselves with these key factors:
Cutting Speed
The rate at which the cutting tool moves through the material, measured in surface feet per minute (SFM). Adjusting cutting speed affects tool life and surface finish.
Feed Rate
The speed at which the workpiece or tool moves during machining, measured in inches per minute (IPM). Proper feed rates prevent tool wear and ensure smooth operations.
Depth of Cut
The amount of material removed in one pass. Deeper cuts increase material removal rates but may compromise tool longevity.
Coolants and Lubricants
Using coolants and lubricants minimizes heat buildup, reduces tool wear, and improves surface finish.
Introduction to CNC Machining
Computer Numerical Control (CNC) machining is revolutionizing the industry, offering unparalleled precision and automation. Here’s what beginners need to know:
What Is CNC Machining?
CNC machining involves using pre-programmed computer software to control machining tools. It enables the production of complex designs with minimal manual intervention.
Benefits of CNC Machining
- Precision: Consistent accuracy across multiple parts.
- Efficiency: Faster production times and reduced human error.
- Versatility: Handles intricate designs and multiple materials.
Common CNC Machines
- CNC Lathes: Used for turning operations.
- CNC Mills: Ideal for milling, drilling, and tapping.
- CNC Routers: Create intricate patterns on wood, plastic, and soft metals.
Safety Considerations in Metal Machining
Safety is paramount in metal machining. Follow these guidelines to ensure a secure working environment:
Personal Protective Equipment (PPE)
- Eye Protection: Safety glasses or goggles.
- Hearing Protection: Earplugs or earmuffs.
- Gloves: Avoid loose-fitting gloves near rotating machinery.
- Clothing: Wear fitted clothing and avoid jewelry.
Equipment Maintenance
Regularly inspect and maintain tools to prevent malfunctions and accidents. Keep cutting edges sharp and ensure proper lubrication.
Proper Training
Familiarize yourself with machinery and techniques before operating. Adhere to manufacturer guidelines and seek mentorship when necessary.
Troubleshooting Common Machining Issues
Even experienced machinists encounter challenges. Here’s how to address common issues:
Tool Wear
- Cause: High cutting speeds, improper feed rates, or poor material choice.
- Solution: Adjust parameters, select appropriate tools, and use coolants.
Surface Finish Problems
- Cause: Dull tools, vibration, or incorrect cutting speeds.
- Solution: Replace tools, secure workpieces, and optimize speed.
Dimensional Inaccuracies
- Cause: Improper machine calibration or thermal expansion.
- Solution: Calibrate machines and monitor temperature conditions.
Future Trends in Metal Machining
The metal machining industry is evolving rapidly. Here are emerging trends shaping its future:
Automation and Robotics
Automated systems and robots are streamlining production, reducing labor costs, and enhancing precision.
Advanced Materials
Machining composite materials and alloys is gaining importance in industries like aerospace and healthcare.
Sustainable Practices
Eco-friendly machining focuses on minimizing waste and using biodegradable lubricants.
Additive Manufacturing Integration
Combining machining with 3D printing offers new possibilities for hybrid manufacturing processes.
Conclusion
Mastering the basics of metal machining is the first step toward becoming a skilled machinist. Understanding machining techniques, selecting the right tools, and adhering to safety protocols are essential. As you gain experience, you can explore advanced concepts like CNC machining and automation, staying ahead in this dynamic field. Metal machining is not just a skill but a gateway to innovation and creativity in manufacturing.
Need an Industrial Machine Shop in Baton Rouge, LA?
Established in 1956, our team here at Metal Works Corporation is an A.S.M.E. certified industrial fabrication company specializing in pipe and tube bending, pipe fabrication, coiling, vessel fabrication, and welding for major industries. Our in house’ machine shop has unique capabilities and produces specialty springs of all alloys, custom rotating mechanical seals, and various other industrial components. We appreciate our customers and work to forge lasting relationships built on trust and reliability. Contact us today and allow our team to be the shortest distance between problem and solution for your unique industrial requirements.